Operations and maintenance policies are defined in plans that meet the following criteria:
- objectives of the specifications of the operations and maintenance contract (minimum requirement);
- as well as the more ambitious objectives defined by the general management of the operator in terms of operational and economic performance.
These plans are genuine operational guidelines for each of the departments concerned. They are drawn up by the managers concerned and validated by the head of operations who oversees overall operational performance, which depends on the combined performance of the operations and maintenance activities.
The operations and maintenance plans have a similar presentation structure and each one clearly defines the activities to be carried out for a given period. They must be consistent with the business plan.
Six topics are generally covered in a plan:
The technical, operational and social context and environment
First and foremost, the plan must be based on the knowledge of the project environment. The description of this environment is essential because it will form the structure on which the operational organisation of the operator is based. This analysis should address the following:
- The service offer: layout of the routes, timetables or intervals, daily service hours, bus stop service;
- Climatic environment: temperature, humidity, etc. ;
- The environment and social regulations, including health, safety and security rules;
- The standard of the road and ground infrastructure (station, bus stop, etc.) ;
- The nature, quantity and standard of the operational facilities: rolling stock, bus shelters, ITS equipment (on-board and dockside), etc.;
- Maintenance and storage infrastructure and facilities: workshop, depot, etc. ;
Objectives, and expected and targeted performance levels
The general framework of the service offering and the level of performance of the operator must be contractually defined in the specifications of the operations and maintenance contract. We will make sure that the expected performance levels are formally defined, measurable and achievable given the specific environment of the project.
A no-claims bonus system, which can be revised with each period, can be set jointly between the Autorité Organisatrice des Transports Urbains (organising authority of urban transport) and the operator. It is set up in order to penalise the operator if the contractual performance thresholds are not reached or pay the operator a share of the profits if the thresholds are attained.
Some performance criteria used in contracts:
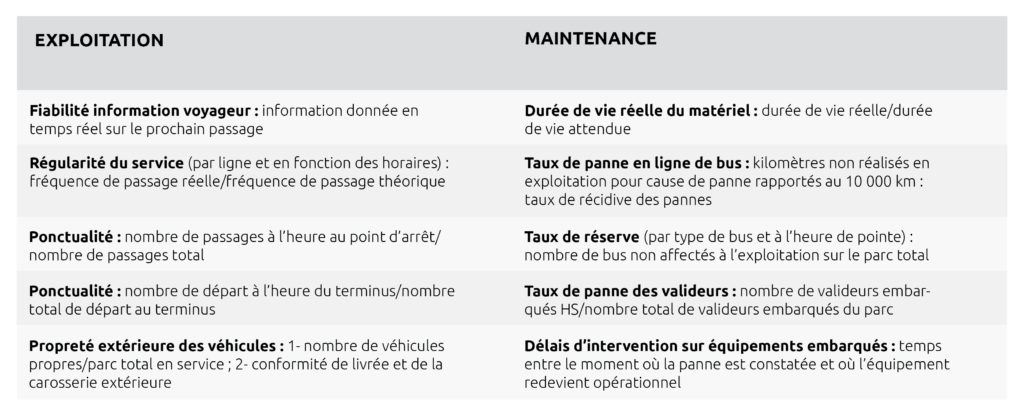
The organisational chart of each operational unit, i.e. operations and maintenance, is drawn up from a functional and hierarchical point of view. It highlights the functional relationships of staff members with cooperative and interdependent duties.
Job profiles, with their required skill level, will also be defined in order to precisely identify each person’s role, as well as the minimum training and experience required for each position.
>Operations will include all the job roles that have a direct link with the production of the service offer: drivers, route regulators, station personnel, operations supervisors and managers, methods and planning officers, etc. Certain peripheral and/or complementary professions and missions may be attached to operations, e.g. commercial agents, title control/verification officers, communication and research staff, etc.
>Maintenance will include all the maintenance roles that contribute to the reliability and maintainability of the infrastructures, rolling stock and operational facilities, including jobs relating to maintenance methods and engineering.
The necessary human and technical resources by type (quantity and quality)
For each job/profession, the necessary quantity will be identified, taking into account the operating constraints, the specific characteristics of the service and the working conditions, by seeking to optimise operability and maintainability. Thus, in order to calculate, for example, the number of drivers required, we will rely on the scheduling and staffing techniques and methods, taking into account the types of day (working day, bank holiday, etc.), the route layouts, the type of service and the operational and social parameters (traffic speed, start and end of service time, regulation time, driving time, etc.).
The procedures and methods to be applied
For each operation and maintenance process, the procedures specify in detail the applicable rules and methods on a daily basis, both during normal operation and in the event of contingencies (disruption for operations/number of breakdowns).
These procedures and methods are updated on a regular basis depending on operational experience (e.g. new equipment), the changes in the social, technical and contractual environment, the recommendations of the manufacturer and the regulations. The management must regularly ensure that the methods and procedures are correctly applied by the operators.
Activity control and monitoring measures
An operational dashboard will therefore be drawn up on a regular basis, i.e. monthly. It will be managed by a management controller who will be responsible for establishing and recording all the data and operational performance indicators, guaranteeing the reliability of the data and highlighting the discrepancies and/or deviations.
Once this has been completed, the dashboard will be a real operational management tool for quickly correcting deviations by implementing appropriate action plans.